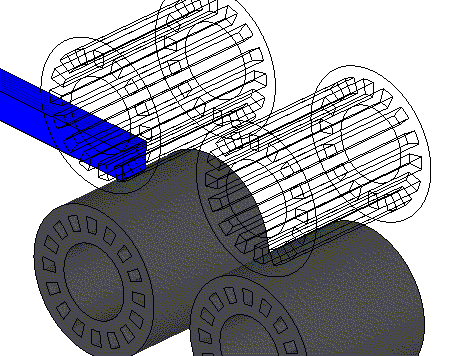
Product Name
Sandblasting
The sandblasting process uses compressed air as a power to form high-speed jets. The spray material (copper ore, quartz sand, corundum, iron sand, Hainan sand) is sprayed onto the workpiece surface at high speed. So that the appearance of the outer surface of the workpiece is changed. Due to the impact of the abrasive on the workpiece surface and the cutting action, Make the surface of the workpiece get a certain degree of cleanliness and different roughness, So that the surface of the improved mechanical properties.
Sandblasting process pre-treatment stage: Means that before the workpiece is sprayed on the protective layer, The workpiece surface should be treated.
Function: remove scales, oxides, oil residues and other burr, improve the mechanical properties of parts, achieve different reflections or matt finishes on stainless steel workpieces.
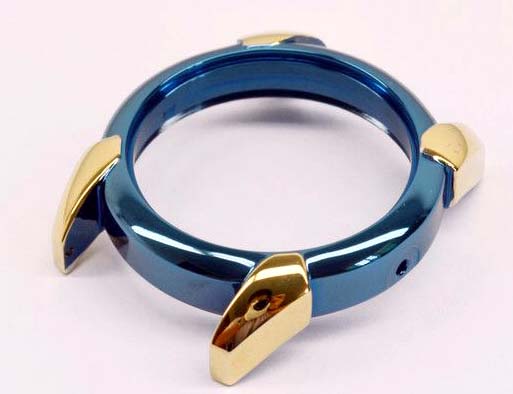
Shot blasting
Shot blasting is the use of a high-speed rotating impeller to throw a small Steel pill at high speed and hit the surface of the part. Therefore, the oxide layer on the surface of the part can be removed. At the same time, steel shots hit the surface of the part at a high speed, causing distortion of the crystal lattice on the surface of the part. Increase the hardness of the surface, It is a method of cleaning the surface of parts. Shot blasting is often used to clean the casting surface or to strengthen the surface of the part.
Function: Shot blasting is to remove surface oxides and other impurities to improve the appearance quality. Can improve the fatigue fracture resistance of material parts, prevent fatigue failure, plastic deformation and brittle fracture, improve fatigue life.
Rolling
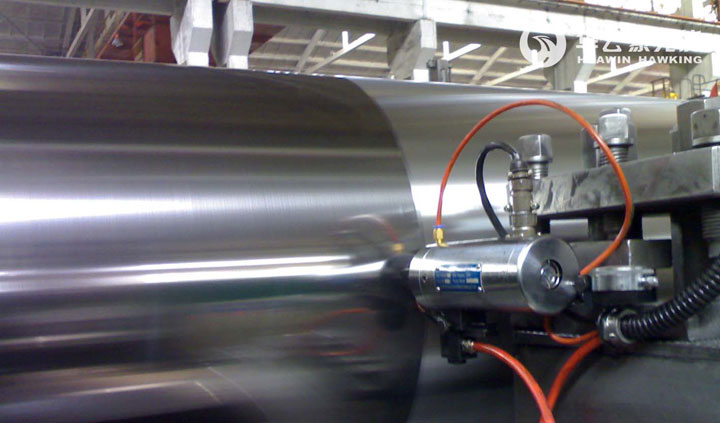
is the process of cutting the surface of a metal part by means of the rotation of a special grinding wheel (or belt) with abrasive material attached thereto. Rolling is suitable for processing all metal materials and some non-metallic materials. The Rolling effect mainly depends on the characteristics of the abrasive, the quality of the abrasive, the rigidity of the Rolling wheel, and the rotation speed of the axle.
Function: Rolling can remove parts of the surface of the burrs, rust, scratches, welds, welds, sand, oxide and other macro defects, in order to improve the flatness of the parts and plating quality.
The order in which the parts of the part are ground is acute angle> edge> outer surface> inner surface. Rolling cannot be used on complex part surfaces. Rolling equipment is low in cost, but it takes a long time and is mainly applied to small hardware parts.
Polishing
Polishing refers to the use of mechanical, chemical or electrochemical effects to reduce the surface roughness of the workpiece to obtain a bright, smooth surface. Polishing does not improve the dimensional accuracy or geometric accuracy of the workpiece, but it is intended to give a smooth surface or a mirror finish, and sometimes to eliminate gloss (extinction). It is the use of polishing tools and abrasive particles or other polishing media to modify the surface of the workpiece.
Stainless steel is widely used due to its high corrosion resistance and decorative properties. Therefore, it is a requirement for the surface treatment to produce such appliances that the harmful substances on the surface must be completely removed.
The materials required for stainless steel polishing generally include: "polishing wax, hemp wheel, nylon wheel, cloth wheel, wind wheel, wire cloth wheel" and so on.
When polishing, the high-speed rotating polishing wheel (peripheral speed of 20m/s or more) is pressed against the workpiece, which causes the abrasive to produce rolling and micro-cutting on the surface of the workpiece, thereby obtaining a bright processing surface. The surface roughness can generally reach Ra0.63-0.01 micron; when a non-greasing matting polishing agent is used, the glossy surface can be matted to improve the appearance. When large quantities of bearing steel balls are produced, drum polishing methods are often used.
Rough polishing is to put a large number of steel balls, lime and abrasives in a tilted can-shaped drum. When the drum rotates, it randomly rolls and collides steel balls and abrasives inside the drum. It is possible to remove the protruding surface of the part. The purpose of reducing the roughness of the surface of the part is to remove the margin of about 0.01 mm.
Satin finish
The process of machining the surface of a metal part using a brush wheel made of metal wire, animal hair, natural fiber or synthetic fiber.
For cleaning parts of the surface, mainly for metallurgical plants sheet plating and painting and other production lines
Flame plating
The paint is atomized by the spray gun and applied to the surface of the object. Compressed air paint, high pressure airless paint, electrostatic spray paint and other methods.
At present there are four main types: arc spraying, flame spraying, plasma spraying and explosion spraying.
Spraying technology can obtain coatings with physical and chemical properties such as abrasion resistance, corrosion resistance, heat insulation, electrical conductivity, insulation, sealing, lubrication, and other special machinery on various substrates.
The wide range of applications mainly include hardware, plastics, furniture, military, ships and other fields. It is the most common coating method used today;
Spraying operations require environmental requirements have 1000000-100 clean room, spraying equipment includes spray guns, spray booths, paint booths, curing ovens/drying ovens, spraying workpiece conveying equipment, mist elimination and waste water, and exhaust gas treatment equipment.
The types of electrostatic spraying can be divided into two categories: pure electrostatic atomization and electrostatic atomization with additional energy.
Electrostatic spraying refers to the use of corona discharge principles. The atomized paint is charged negatively under the action of a high voltage DC electric field, and it is adsorbed on the surface of the positively charged substrate to discharge the coating method. Electrostatic spraying equipment consists of spray guns, spray cups, and electrostatic spray high voltage power supplies.
Electrostatic spraying is based on the principle of electrostatic attraction, that is, the grounded coating is used as the positive electrode, and the oil atomizer (ie, the spray cup or spray plate) is connected to high voltage as the negative electrode.
PREVIOUS:NONE
NEXT:Chemical Surface Treatments
NEXT:Chemical Surface Treatments